It is essential to generate a target trajectory that suppresses residual vibration and torque in order to achieve high-speed and high-precision positioning in a multi-inertia system such as a table system where resonance occurs. However, in the trajectory generation method by final-state control (FSC), which is one of the target trajectory generation methods, there is a possibility that the calculation time will increase significantly as the travel time in the generated trajectory increases.
Therefore, we are conducting research on trajectory design using deep learning (DL). We are developing an optimal trajectory generation filter to generate trajectories equivalent to ones generated by FSC.
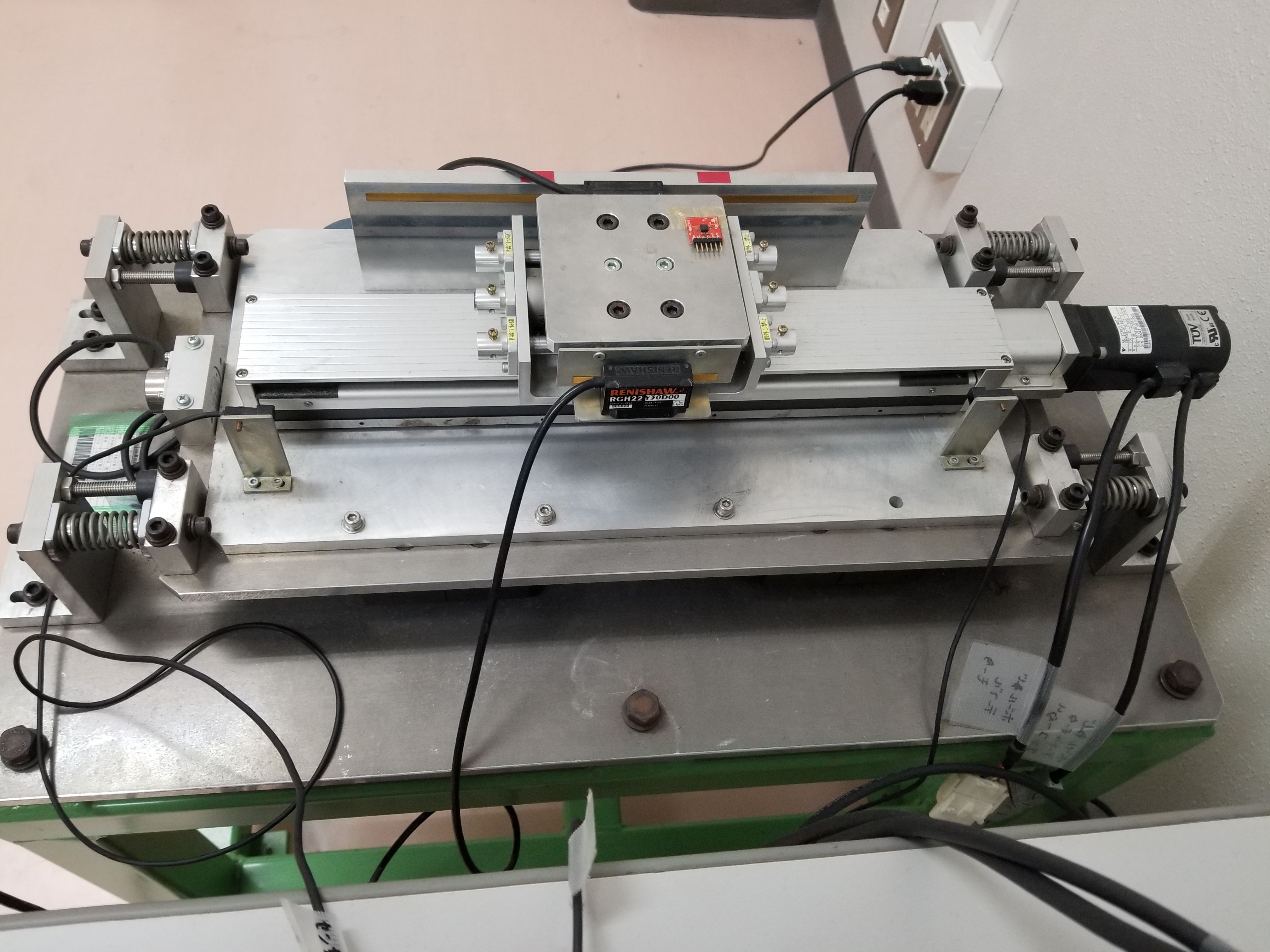
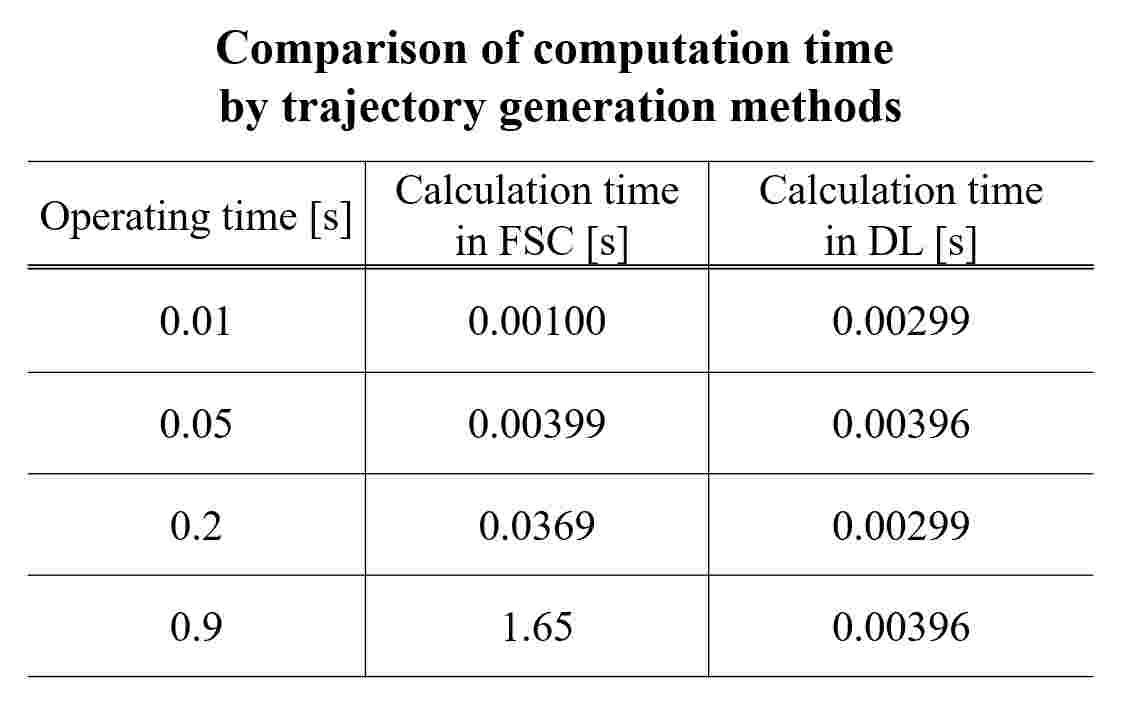