RESEARCH
Study on liquid fuel production process from woody biomass waste (Biomass to Liquid, BTL)
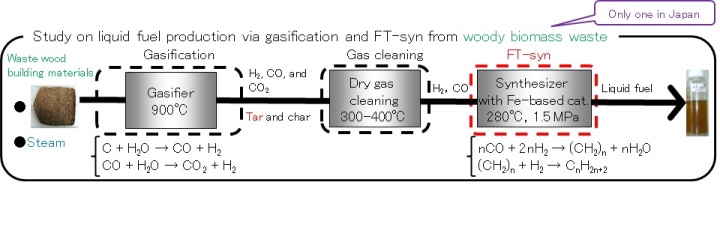
Gasification of waste wood building materials
There are five million tons of waste wood building materials in a time
span of a year in Japan. 50% of the energy used in a waste wood building
materials recycling plant is light oil used as the fuel for a heavy machine.
The production of this light oil from waste wood building materials promises
not only the recycling promotion but also the reduction of CO2 emissions.
However, wood building materials used from 1960's through until 2000's
are treated with preservatives or pesticides using CCA (copper chromated
arsenate). The investigation of the phase and substance behavior of arsenic
in the gasification of waste wood building materials is required because
arsenic may cause adverse effects on a living organism, gasifier, and FT
(FischerTropsch) catalyst.
In the study, an optimum gasification condition for the H2/CO molar ratio
of 2 in the gasified gas of waste wood building materials and the phase
and substance behavior of arsenic (As) in the gasification for the purpose
of liquid fuel production were investigated through the use of a fixed-bed
reactor under the conditions of the H2O/C molar ratios of 0.5-2.6 in the
feed and the temperatures of 600-800 ºC.
Dry gasification gas cleaning using waste wood building materials char
The fuel gas from gasification processes contains various amounts of impurities
and particulate originating from the solid fuel and attrition products
from the bed material. Hot gas cleaning also implies chemical manipulations
of the product gas to meet environmental as well as technical standards.
High molecular weight products, tars, and other components like alkali
trace elements may cause in the condensed phase severe operational problems.
These have to be removed before the gas product can qualify as fuel for
gas engine or gas turbine purposes.
From these backgrounds the research plan is development of Hot Gas Cleaning
from wood waste building (Biomass) Gasification, various method for tar
removal have been investigated in the different range of gas cleaning temperatures.
At low temperatures, <403K, the tar was removed by cooling with water
or adsorption on adsorbent. At high temperatures, 873 to 1173 K, it was
cracked by catalysts such as Ni/Al2O3 and dolomite .
Activated carbons as an adsorbent are extensively used to remove pollutants
from exhaust gases at low temperatures . Some researchers removed organic
pollutants such as polycyclic aromatic hydrocarbons (PAH) generated from
combustion process by the adsorption to activated carbon at 423K. On the
contrary, the method for tar removal at medium temperature ranging from
473 to 773 K has several advantages compared with other methods (Hamelinck
et al, 2002). Compared with the tar removal methods at a low temperature,
this method has the following advantages: (1) the drain could be treated
more easily, and (2) in the synthesis of liquid fuels using producer gas
from biomass gasification, the method can supply the gas to the liquid
fuel synthesis process without cooling below the required temperature (473-573K).
However, the tar removal at medium temperatures of 473 to 773K was hardly
reported using carbonaceous materials. In the research plan, the hot gas
cleaning of producer gas generated from waste woods, such as waste wood
building material, gasification will be investigated using char produced
in their gasification. Various carbonaceous materials as a bed additive
will be used to compare the ability of tar removal at the medium temperature.
Fischer-Tropsch synthesis for liquid fuel production from waste wood building materials
Light oil for diesel fuel mainly consists of n-paraffin. In FTS, olefin
is relatively much produced with an Fe-based catalyst, whereas paraffin
is relatively much produced with a cobalt (Co) -based catalyst. Thus, a
Co-based catalyst has an advantage for the production of light oil by FTS
from a viewpoint of desired products. However, the cost of an Fe-based
catalyst is generally lower than that of a Co-based catalyst. This allows
an Fe-based catalyst to produce paraffin by the hydrogenated reaction in
another reactor after olefin production by FTS.
In the present study, the FTS of syngas using an Fe-based catalyst is experimentally examined in terms of the primary light oil yield and carbon mass balance in order to produce HCs such as diesel fuel. The effect of the chemical species, such as potassium as a promoter, included in the Fe-based catalyst on the FTS is investigated.
Environmental and economic analysis of liquid fuel production process from woody biomass waste
Recently, some researchers have conducted experimental studies on the synthesis
of liquid fuels via woody biomass gasification. In addition to technical
research and development, the environmental and economic analysis of this
process is required for commercialization. In this study, gasification
by external heating (i.e., only with steam) is adopted and focused on heat
and power resources. From an economic viewpoint, the use of inexpensive
heat and power resources results in a low production
cost, while the supply of external heat and power by fossil resources does
not lead to CO2 reduction. In the present study, the process is designed.
The light oil yield and energy recovery rate in the processes and the amount
of input energy for the processes are investigated. In addition, the environmental
and economic analysis of the processes is performed from the viewpoint
of CO2 emission and capital and operating costs.
Study on application development of waste wood building materials tar to recycled asphalt
emission and capital and operating costs.
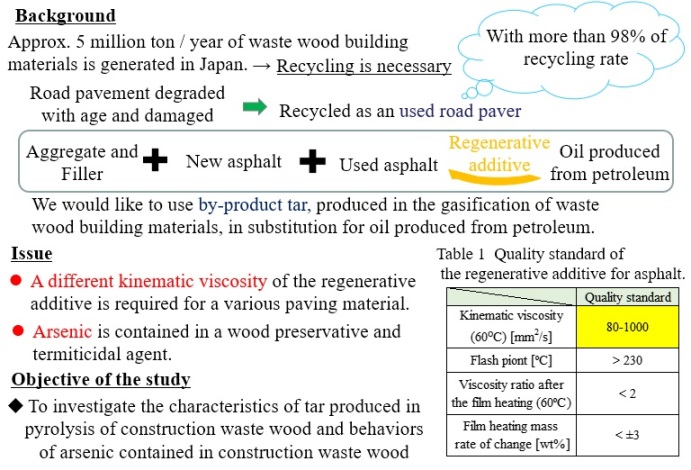
Study on application development of recycled CFRP waste
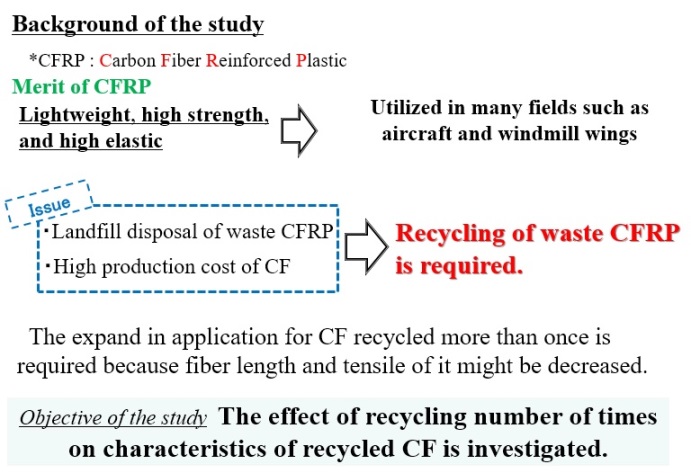